Ring Die Pellet Mill
The capacity ranges from 200 kg/s to 3 tons per hour. It is widely used for processing wood, straw and other biomass materials. It features in high performance, low cost, long life and easy maintenance. The key parts are made of alloy steel. And the die is made of stainless steel.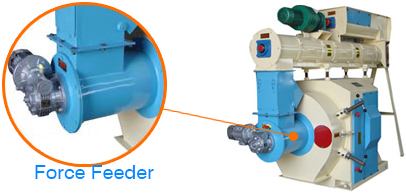
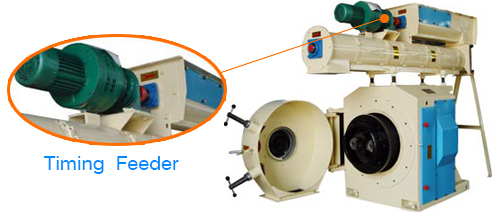
Model | Main motor power(Kw) | Capacity(t/h) | Feeding motor power(Kw) | Conditioner motor power(Kw) | Diameter of die(mm) | Pellet diameter (mm) |
---|---|---|---|---|---|---|
KMPM25 | 7.5*2 | 0.2-0.3 | 0.75-0.55 | 2.2 | 250 | 4-8 |
KMPM32 | 37 | 0.3-0.6 | 0.75-0.55 | 2.2 | 320 | 4-8 |
KMPM35 | 55 | 0.5-0.8 | 0.75-0.75 | 2.2 | 350 | 4-8 |
KMPM40 | 75 | 0.7-1.1 | 1.5+0.75 | 2.2 | 400 | 4-8 |
KMPM42 | 110 | 1.0-1.5 | 1.5+0.75 | 5.5 | 420 | 4-8 |
KMPM508 | 132/160 | 2.0-3.0 | 1.5+0.75 | 7.5 | 508 | 4-8 |

Some Details of Other Pellet Mill Equipments
Our company can provide single pellet mill equipment for your complete pellet mill line. If the size and moisture of your raw material is changeable, the pellet equipments are necessary in the wood pellet plant. Moreover, these machines also can make higher quality wood pellet comparing to one unit wood pellet mill only. Since the crusher and dryer can make the size and moisture of your raw material evenly and most suitable for further pelletizing.
All these pellet equipments have some models which can be chosen according to the character of your raw material. And also for the conveyors, it also can be designed according to the size of your workshop.
The hammer mill is a machine whose purpose is to crush materials by the collision between the high-speed hammer and materials. It is suitable for milling raw material like tree branch, cotton stalk, corn stalk, wheat straw etc. with size less than 50mm (diameter). After milled, the output size can reach diameter 3-5 mm, then it is suitable for further processing.
The fundamental theory is simple. A hammer mill is actually a steel drum consists of a vertical or horizontal rotating shaft or drum on which hammers are mounted. The hammers swing on the ends of the cross freely, or fixed to the central rotor. The rotor is spun at a high speed inside the drum while material is fed right into a feed hopper. The material is impacted by the hammer bars and is thereby shredded and expelled through screens in the run of a selected size.
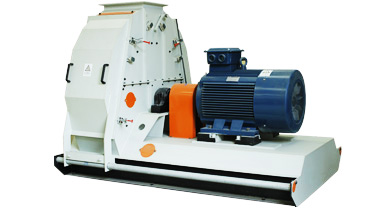
Model | MFSP56*60 | MFSP70*60 | MFSP66*80 |
---|---|---|---|
Powder(Kw) | 37 | 75 | 90 |
Capacity(f/h) | 1 | 2 | 2.5 |
The rotary dryer is used to reduce the moisture content of the raw materials before pelletization. The machine is designed to work continuously and automatically, and includes a rotary dryer, screw feeder, cyclone air system, air lock and fan.
The wet material enters the dryer through the feeder in controlled quantities. A rake inside the cylinder distributes the material uniformly in the dryer for maximum exposure to the current of hot air. After traversing the length of the dryer the material is discharged through a star valve at the end with the perfect moisture content.
The rotary dryer may also require a hot blast stove as a source of hot air. The stoves fuels can be the same biomass materials—wood, wood pellets, straw, etc.—bound for pelletization.
Model | Diameter (mm) | Length(m) | Power(kw) | Speed of rotation (r/min) |
---|---|---|---|---|
HZG6 | 600 | 4、5、6、7、8 | 3-3.5 | 3-20 adjustmen |
HZG8 | 800 | 4、5、6、7、8、9、10 | 5.5-7.5 | |
HZG10 | 1000 | 6、7、8、9、10、11、12 | 5.5-7.5 | |
HZG12 | 1200 | 6、8、9、10、11、12 | 7.5-11 | |
HZG15 | 1500 | 8、10、12、14、16、18 | 11-15 | |
HZG18 | 1800 | 8、10、12、14、16、18、20 | 15-18.5 | |
HZG22 | 2200 | 10、12、14、16、18、20、22、25 | 18.5-22 |
Item(m) | Capacity(t/h) | Speed of rotation (r/min) | Motor power (kw) | Angle (degree) | Temp of final |
---|---|---|---|---|---|
f1.0x5.0 | 0.5-1.2 | 0.6-6 | 4 | 3-5 | =1.5% |
f1.2x6-10 | 1.5-3 | 0.6-6 | 5.5 | 3-5 | =1.5% |
f1.5x12-18 | 3-3.5 | 0.6-6 | 15 | 3-5 | =1.5% |
f1.8x12-18 | 5-6.5 | 0.6-6 | 18 | 3-5 | =1.5% |
f2.2x12-22 | 7-12 | 0.6-6 | 22 | 3-5 | =1.5% |
f2.4x15-20 | 9-15 | 0.6-6 | 30 | 3-5 | =1.5% |
f3.0x25 | 16 | 0.6-6 | 55 | 3-5 | =1.5% |
Our counter flow cooler adopts the advanced international counter-flow cooling technology, which make pellets cool full and uniform. Unique slide valve discharging mechanism makes nesting smooth and reliable operation. After cooling, the pellets temperature is no more than room temperature 3 ℃ -5 ℃, and the precipitation rate is not less than 3% -3.5%. The temperature must be quickly cooled down, and the moisture content must be reduced to less than 12 percent for storage and handling. Our cooler can manage both of these processes simultaneously.
Model | SKLN 14 | SKLN 19 | SKLN 22 |
---|---|---|---|
Cooling Volume (m3) | 2.5 | 5 | 8 |
Output (t/h) | 1-2 | 3-5 | 6-8 |
Air-absorbed (m3/h) | 10000 | 15000 | 27000 |
Power (kw) | 3 | 3 | 2.5+1.5 |
Packing is the final process in pellet production. This automated machinery is comprised of storage bins and a sealing machine. The computerized system weighs the finished pellets before sealing, then discharging the bags. A conveyor moves the bags for storage at the desired location.
This is an automatic bagging machine. It is composed of a quantitative packing electronic scale, a hemming machine and a conveyor heat-sealing machine. The quantitative packing electronic scale includes feeding part, filling part, and weight control meter systems.
While these pellet mill equipments will release greatest potential in the complete wood pellet line. The complete wood pellet line is combined with process as pulverizing, drying, pelletizing, cooling and packing. We provide wood pellet plants which are tailor-made, economical, efficient solution with latest technology.
Add:Suite E, 3/F, Jinhao Business Bld., Renmin Rd. Anyang, Henan, P.R.C
Tel: 0086 372 5953961
FAX: 0086 372 5951936
E-mail: info@pelletmillequipments.com